An interesting and fascinating trip is one made through the #8 Colliery of the Lehigh Navigation Coal Company outside of Coaldale, Pennsylvania.
The tunnel of the mine was started in 1845. The first shaft was sunk in 1909 and the last level (8th level) was made in 1928-29.
The mine descends 1237 feet, which is 165 feet below sea level. For each ton of coal taken from the mine, 20 tons of water are pumped out by the main pump. Some of the water is corrosive necessitating the use of huge wooden pipes to carry it off. In places, small waterfalls of alum and sulphur water turn the walls into shades of bright yellow and orange.
The large pumps work day and night, automatically pumping the water out of the gangways. Eighty mine cars of silt are taken from the sump every six months.
Abandoned mine shafts are reservoirs of water to be pumped to the surface. It is not out of the ordinary for these shafts to be filled with water 500 feet deep.
The 8th level has the coal veins Mammoth, Forty Foot, Primrose, Orchard, West and East Top.
Most of the coal miners have worked many years in the mines. Our guide, William Laird Henry, started in the mines at 13 ½ years of age and has worked at coal mining for 44 years. William Smith has been in mining for 30 years.
An interesting experience was the blowing of the face in the #10 breast where miner Andy Mackay worked. Andy and his partner worked 7 or 8 months digging a 60 foot passage up into the coal vein. They have been working 2 months in this vein which now is a room 30 feet high. They place dynamite (about 4 pounds in each hole) in the wall, then retire down the chute to the gangway from where the charge is set off. After the blast, the section is allowed to settle until the next morning. The Fire Boss, Martin Polansky, arrives early in the morning and inspects each blasted section for the presence of poisonous gas and safety conditions. Only then are the miners allowed to return to the dynamited area to continue working.
After coal is transported out of the mine it is taken to the rotary dumper. The dumper handles two mine cars at one time, turning them bottom side up spilling the coal into a huge chute from which it goes into breaker conveyor cars holding 20 tons at one time. Then these cars carry the coal up 8 floors on the outside of the breaker and dump the load at the top floor. The coal then travels down the 8 floors in chutes filled with a constant flow of water to wash the coal through the shakers for grading.
The shakers are long strips about 3 feet wide which are perforated with holes for various sizes of coal. The large perforated strips are placed on the top with the next size perforated strip below in shelf-like arrangement. The shaker automatically shakes the coal pieces across the strip, retaining the large pieces and releasing the smaller pieces to fall through.
This graded coal is carried to storage bins from where it is loaded into railroad gondolas. The finest grade of coal is barley grade.
The barley size coal is washed through a trough where lubricating oil and pine oil are mixed with it. Then it is carried out into a tremendous sized vat where large whirling paddles scoop the fine mixture off into a chute where it is collected for shipment.
Barley coal is burned in the stoker-fed furnaces such as in use at the Hometown plant.
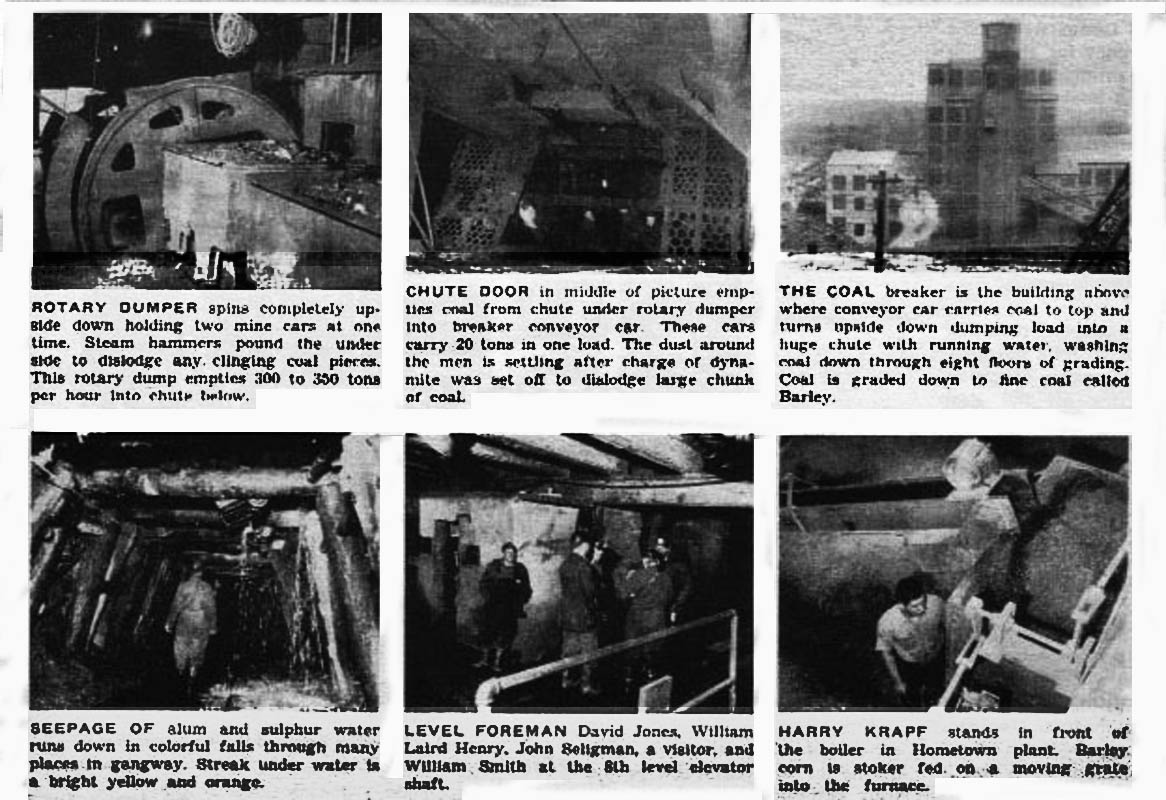